Experiential Design & Fabrication
We help NYC filmmakers, brands and experiential marketing agencies create unforgettable experiences. For over 40 years, we've been providing prop and scenic fabrication, graphics and prop rentals to film & television, live theater & events, retail, pop-ups, mobile tours, trade shows, and experiential marketing. Have a project for us?
REQUEST A QUOTERecent Fabrication Projects
Chances are you've seen our work during your last streaming binge or while strolling past the window displays on 5th Avenue
You're in Good Company
We work with big brands, artists, designers and experiential marketing agencies
Our Fabrication Capabilities
Our team of artists, craftsmen, engineers, and programmers are fully equipped with the latest technology
Our Graphics Capabilities
Our graphics and print capabilities support brand activations, experiential environments and prop fabrications
Recent Film & TV Credits
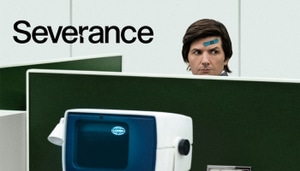
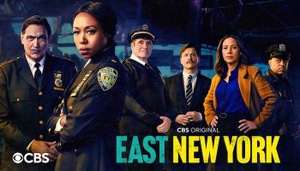
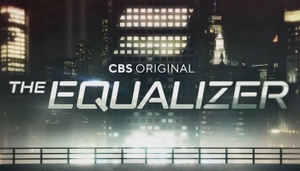
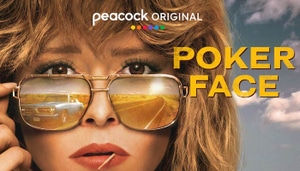
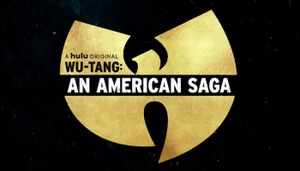
Let's Build Your Next Project
Our team is ready to help you bring your ideas to life
REQUEST A QUOTEVisit our Fabrication Studio & Prop House
Visit Us
Open Monday - Friday, 9am - 6pm Loading dock available. Call in advance for parking assistance.